Smart surgical tool enables enhanced precision
A new 'smart' surgical tool has been developed that could help doctors perform delicate tasks with enhanced precision.
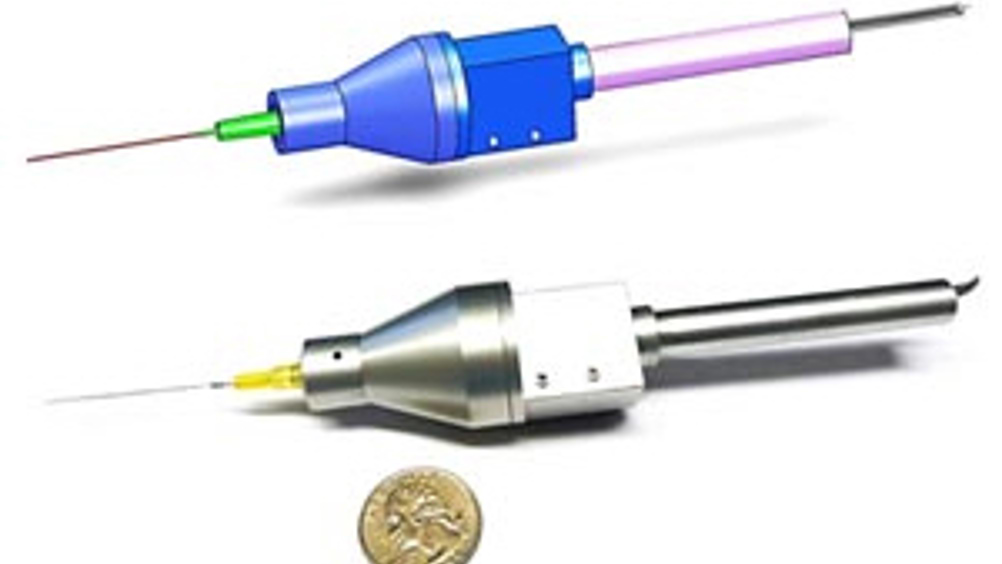
Utilising a specialised optical fibre sensor, the tool compensates for unwanted movement by making hundreds of precise position corrections each second – fast enough to keep the surgeon's hand on target.
The device combines an optical coherence tomography imaging technique as a distance sensor with computer controlled piezoelectric motors to actively stabilise the tip of the tool.
"Microsurgery relies on excellent motor control to perform critical tasks," said Cheol Song, a postdoctoral fellow at Johns Hopkins University. "But certain fine micro-manipulations remain beyond the motor control of even the most skilled surgeon. At its most steady, the human hand naturally trembles, moving on the order of 50-100 microns (about the thickness of a sheet of paper) several times each second."
Because the single fibre optic cable is so small and flexible, the researchers were able to easily integrate it into the front of a tool used for eye surgery. By continually sending and receiving the near infrared laser beams, the high-speed fibre-optic sensor precisely measures the motion of the probe.
This information then feeds to a computer that sends signals to small piezoelectric motors integrated into the surgical device to control the position of the tool tip. This creates a series of 'station keeping' maneuvers that compensate for the surgeon's hand tremors.
Combined, the sensor and motors can operate accurately at 500hertz, higher than the typical tremor frequency of 0 to 15 hertz.
During the next few years, the researchers hope to take their instrument from the laboratory to the operating suite, and with additional refinements expand its use to other fine-scale surgeries.