Prototyping used to be the primary use for 3D printers, but now they are a common sight on factory floors. Manufacturers have adopted additive manufacturing for the ability toefficiently create jigs, fixtures, and low-volume parts. Traditionally CNC machines would have been used for all of these tasks, though with low-volume production the costs could be prohibitive. By comparison, Markforged 3D printers will reliably work unmanned through the night and over the weekend, and the material and setup costs are far smaller.
Continuous Fibre Reinforcement (CFR) is critical for industrial applications. The FX10 for example lays continuous filaments of carbon fibre, cutting them exactly to measure and “ironing” them into the base material. This is what gives Markforged 3D printed parts the strength to survive the extreme forces inside CNC machines, and with proper design you can achieve better strength-to-weight ratios than aluminium. This free design guide shows you how to do this, and acts as a “cheat sheet” for 3D printing.
See how easy the FX10 is to use in this video.
End use parts are also a common application for Markforged 3D printers. With industrial drones, racing cars, satellites and aircraft all using 3D printed parts, it just goes to show that additive manufacturing is a proven, mature technology. Even the U.S. armed forces are manufacturing military vehicle parts using Markforged 3D printers, with one U.S. Army unit saving over $244,000 in costs with just one application.
Metal 3D printing another fascinating concept, and there are a huge number of different technologies available. Most metal 3D printers work with a loose powder bed that comes with all sorts of health and safety concerns, but the FX10 is a filament based metal printer. Because the metal is bound inside wax and polymer in a spool and extruded like a normal FFF/FDM printer, the FX10 is far safer and easier to use.
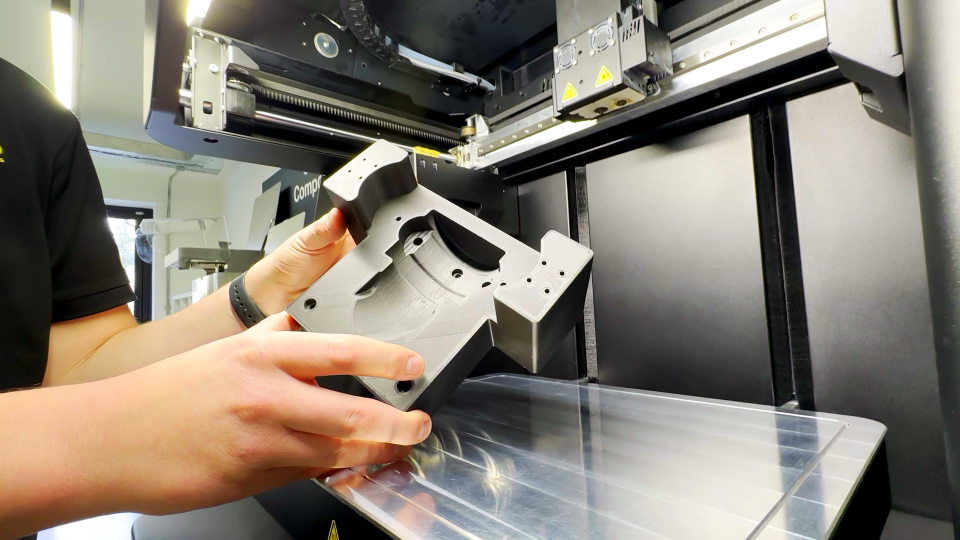
The applications for metal 3D printing are far reaching. While reinforced composites are corrosion resistant and can be used for custom robot grippers, some applications demand the full strength of steel. Dixon Valve in the US have had great success 3D printing metal gripper tools, reducing not only the cost of manufacturing but also improving their designs, allowing for much faster retooling.
Guhring UK have also had great success 3D printing precision PCD cutting tools. Traditionally low-volume special tooling was cost prohibitive for smaller customers, and it could take weeks to design and deliver prototypes. By 3D printing both prototypes and end use products from tool steel, they were able to reduce the cost of low-volume tooling by 75% and lead times by 66% for their customers. You can watch Guhring UK’s story in this video.
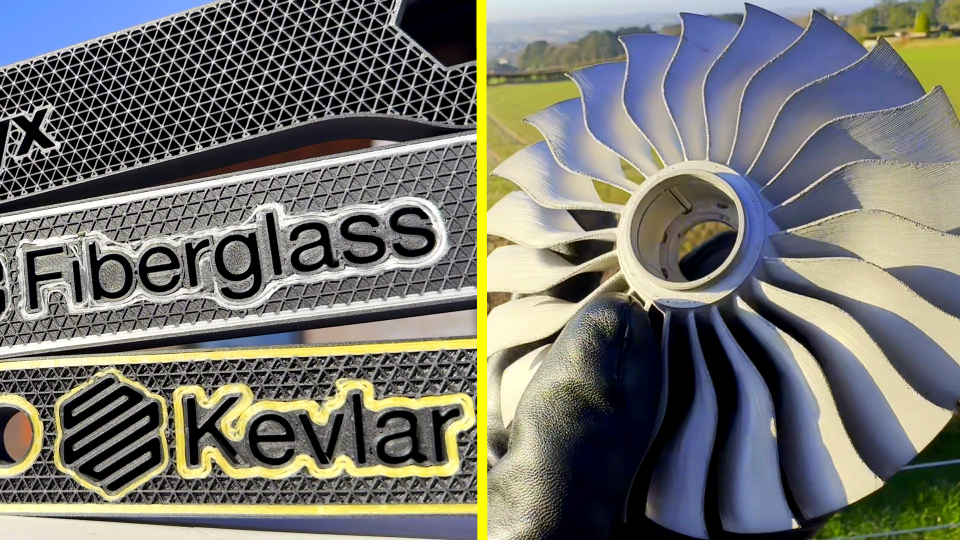
The Markforged FX10 is an impressive machine in it’s own right as well. With a large print bed, down to 50 micron layer height, a heated build chamber and laser micrometre, the FX10 is one of the most reliable and quality focused 3D printers on the market. Here are some of the key specifications:
In so many of these examples the return on investment is clear. So why aren't you 3D printing yet?
You can use this guide on the economics of 3D printing to find opportunities in your own factory. If you'd like a free sample part or a live demonstration, get in touch with Mark3D UK today.